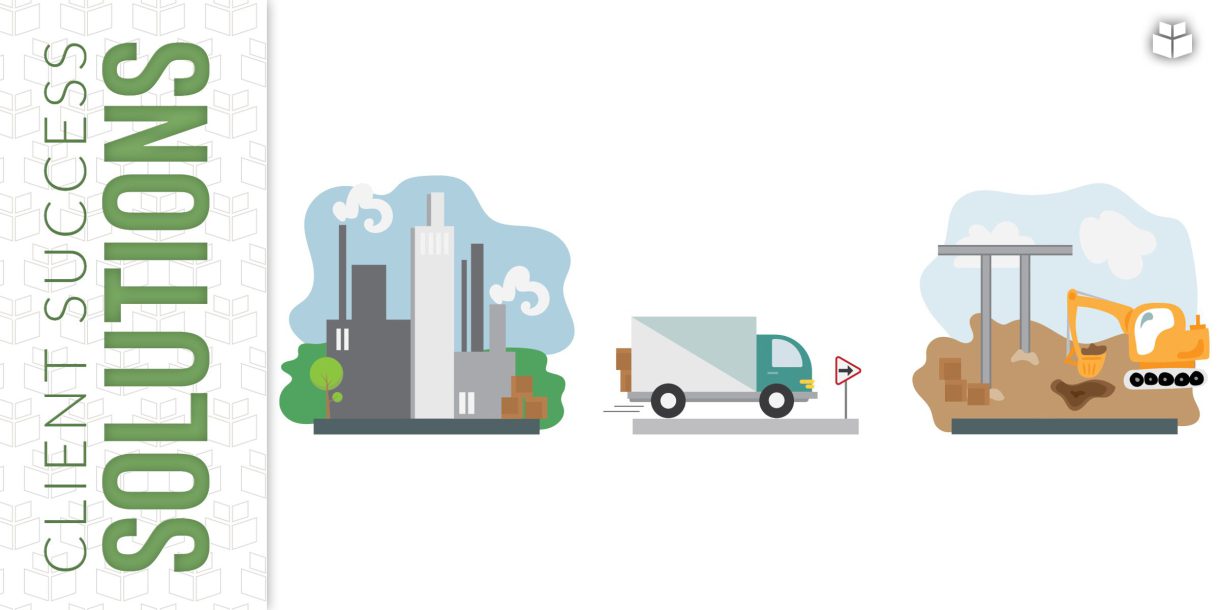
It’s not your imagination the price tag for many items has been going up. Consumer prices jumped 5 percent for the 12-month period ending in May, much higher than the 4.2% increase reported in April. Supply chain disruption across various sectors of the economy has been a primary factor, along with an increase in demand after a subdued year of spending driven by the pandemic.
As vaccinations help propel business openings and the economy, this inflation is being felt acutely in the Architecture, Engineering and Construction (AEC) arena.
Before the news of the consumer price spike, the AEC sector’s fears were reflected in findings by Dodge Data & Analytics, a leading provider of commercial construction project data. In Q4 2020, Dodge’s The Civil Quarterly (TCQ) reported that fewer than half (43 percent) of civil contractors believed fluctuations in the cost of construction materials had impacted their projects at the time.
An April 2021 Q1 report, however, revealed a stark contrast to those findings. The vast majority of respondents have negatively felt these impacts, with 71 percent of civil contractors experiencing serious issues getting materials for projects. Additionally, 76 percent now expect effects from cost increases for construction materials over the next six months.
That WithersRavenel’s clients public and private will feel the effects of these disruptions and cost increases is obvious.
The combination of COVID-19, major storms in 2020, transportation impediments, labor shortage/reduction (due to required social distancing at the workplace, lack of child care, and stress on the system), and increased demand, created the perfect storm of widespread material shortages,says Monica Chevalier, WithersRavenel’s Funding and Asset Management Project Manager. For example, the ice storm that knocked out power in Texas further backlogged the PVC pipe supply. Plus, construction prices are skyrocketing.”
For businesses starting or planning new projects, it is vital to factor delays in procuring construction material and equipment into their schedule. AEC firms with projects already underway need to be diligent about recording delays caused by shortages.
According to Chevalier, in construction there is shortage and subsequent delivery delays of lumber, metals, and plastics. Additionally, staffing shortfalls have been reported among truck drivers and construction contractors.
These delays have caused a domino effect for projects under construction. From bidding twice to get a minimum of three bidders, delays as long as 12 to 16 weeks in some materials affect contract and Notice to Proceed execution, says Chevalier.
If contractors signed the NTP now, they’re locked into the estimated number of days for substantial and final completion, or potentially face liquidated damages. Funding agencies have strict deadlines that need to be met, and don’t always understand what is happening on the ground,she says.
To avoid getting caught up in such situations, Chevalier says, it is imperative to be diligent about keeping records throughout the process.
To provide justification to the funding agencies about legitimate delays, and to avoid penalties for not being on schedule, construction contractors (and their vendors, material suppliers, and subcontractors, etc.) need to document NOW the issues they are having so they don’t have to scramble later,Chevalier says.
Keep track of phone logs, memos on vendor letterhead, emails from vendors, etc. When in doubt, document the issues. I know folks are tired of hearing about €˜unprecedented’ situations, but that is what is happening,she says.
To help you navigate this challenging period of supply chain disruption, increased demand and cost, our Funding and Asset Management team can provide the guidance to ensure compliance, while also helping you plan for delays and advising how to factor those into your project plans.
Reach out to Monica Chevalier reach at (919) 280-0643 or mchevalier@withersravenel.com if you have concerns about funding compliance and for other questions about funding.