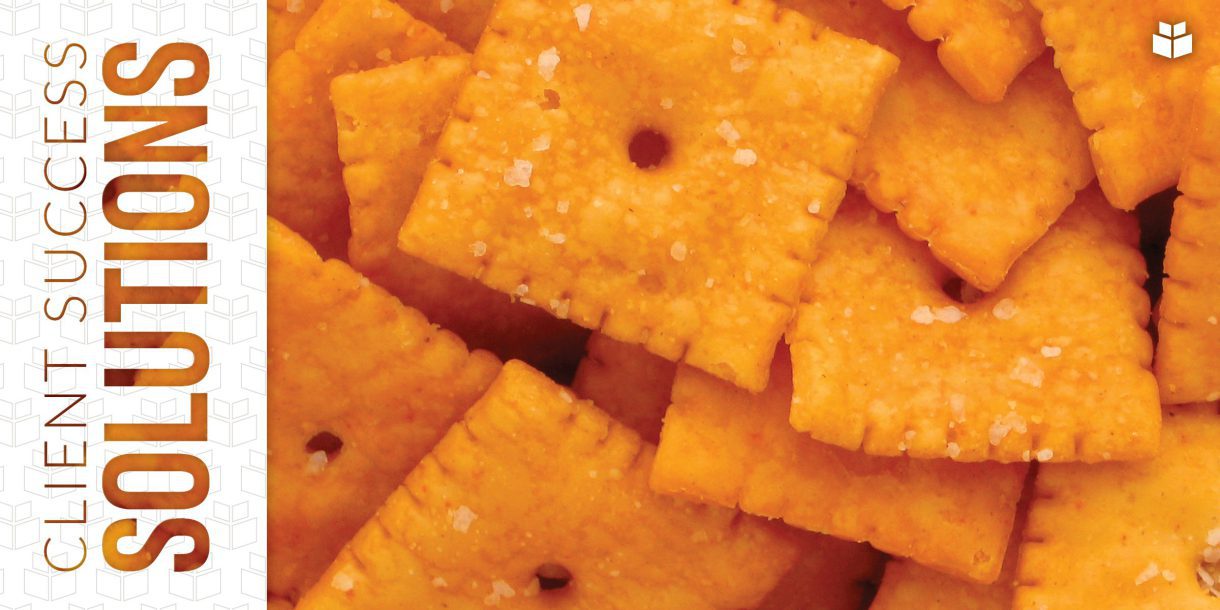
What do WithersRavenel and Cheez-It have in common? A unique project in Cary that helps Kellogg’s properly install massive ovens for baking the popular snack.
The Kellogg’s dilemma? At its Cary plant, the company was planning to replace some ovens in its 300-foot-long oven room. To get the necessary degree of precision, Kellogg’s reached out to WithersRavenel to provide specialized surveying services.
WithersRavenel utilized three different survey tools and methodologies to collect the data Kellogg’s needed: conventional, photogrammetry, and terrestrial 3-D laser scanning.
The conventional survey was a challenge in the oven room. The intense oven heat caused the surveyors to see heat waves, much like what you see rising from a hot road in the summertime. Luckily for our survey technicians, they utilized a robotic total station to lay out the datum lines. The robotic total station can identify the lines and stay locked on the survey rod, adjusting through the fluctuations and providing a more accurate measurement than the human eye in such harsh conditions.
The two 300-foot lines provided placement positions for the installation of brass reference markers set at regular intervals. Those markers were then used as reference points, ensuring the proper alignment of the new equipment. After the installment of the replacement ovens, the markers can continue to serve as landmarks for future considerations.
Additionally, WithersRavenel completed an Unmanned Aircraft System (UAS) photogrammetry survey flight of the outside of the facility, with specific attention to the roof. This specific UAS consists of a quadcopter drone equipped with a high-resolution camera. The UAS drone will fly over the target area snapping photos as it systematically overlaps each pass over the building. The photos can then be stitched together using principles of photogrammetry to create an orthorectified image map of the rooftop.
The goal was to provide rooftop equipment mapping to facilitate new equipment installation, so that Kellogg’s could compare the mapping info to its records on file, overlaying existing CAD files with the new ones. The three biggest advantages to using drones for the roof survey were time, safety, and comprehensive rooftop data. WithersRavenel was able to complete the flight quickly, with none of the danger associated with long-term work on the plant’s roof. Meanwhile, the drone offers millions more data points than conventional surveys, providing a bounty of information with accuracy critical to the manufacturer.
Another service WithersRavenel is providing for the plant is a floor flatness report. Once again, laser scanning comes into play. By taking 360-degree imagery of the oven room’s interior, we’ll be able to put together a color-coded heat map that will show any low spots.
Kellogg’s also requested a way of checking and identifying the facility floor for flatness. The solution was to provide a 3-D high-definition terrestrial laser scan of the floor. A 3-D high-definition terrestrial laser scanner uses Light Detection and Ranging (LiDAR) technology to generate three-dimensional information about its surroundings. A 3-D laser scanner can blanket the area with millions of lasers per second as its lens rotates around its fixed position. The scanner is then moved from one position to another until all the project area data is collected. The different scan positions are then fit together in a process called registration to form a single point cloud of all the data precisely joined. Once the point cloud is registered, the floor can be extracted, and measurements can be taken to identify low and high spots on the floor.
To easily visualize the floor elevation deviations, the point cloud can be colorized by elevation at a user-defined interval and different colors assigned to each elevation. This elevation heat map can easily illustrate areas where the floor rises or falls and the associated elevation, allowing the company to make spot-on adjustments as needed to its production facility.
So next time you enjoy some Cheez-Its, know that WithersRavenel and its technology played a part in Kellogg’s process! Can we put our photogrammetry and LiDAR skills to work for you? Contact Karen Shank at kshank@withersravenel.com.